既存技術と新規技術の
シナジーで生み出す新製品
Iが所属する新規ビジネス製品開発室は、社内外の技術を組み合わせて世の中にない技術に昇華させ、すべり軸受以外の技術創出・新製品としてのアウトプットをする部署である。Iが、市場動向の調査や部署内での検討を経て開発することとなったのが、水処理装置だった。大同メタルは軸受の製造過程で工業用水、純水を使用しており、生じた排水は排水処理施設で処理している。そのため、排水再利用化も純水製造コストの削減も、大同メタルにとって大きな関心事の一つであった。そのときに目に留まったのが自社製品の電極シート(デルエコー®)だった。電極シートはリチウムイオンキャパシタなど電池向けの部品で、液体に含まれるイオンを捉えることができる製品。これを応用し、水の中に含まれるイオンを吸着して水処理ができるのではないかと考えた。しかし、社内に水処理に関する知見はなく、ゼロからのスタートだった。
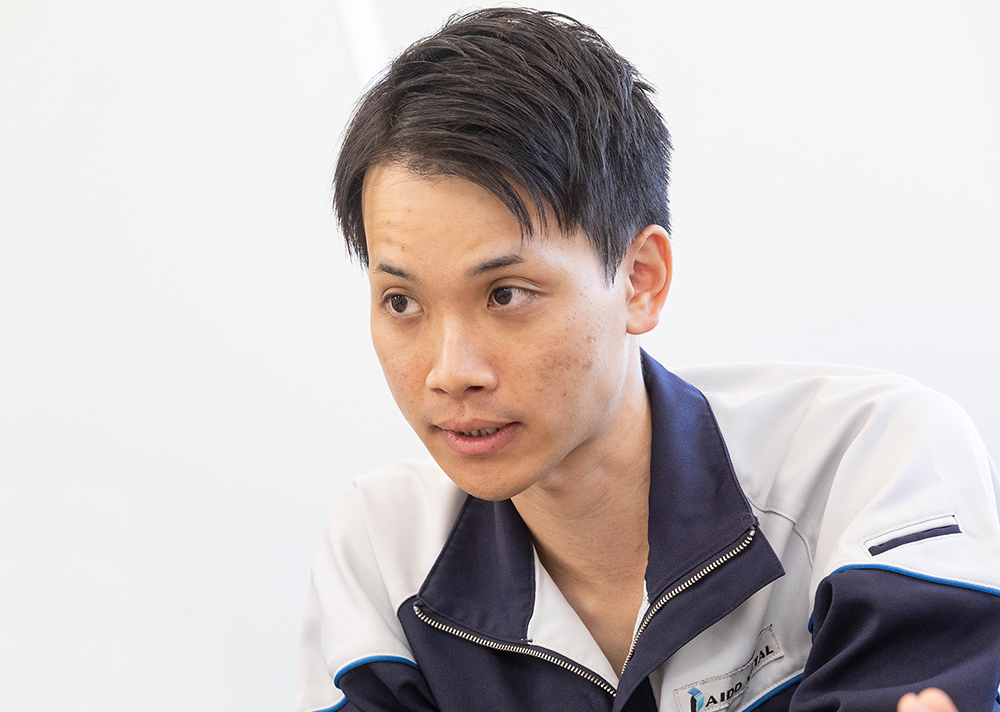
社内テストという試練
まずは電極シートの水処理能力を知るべく、水道水や工業用水、めっき処理排水、溜め池など社内10か所以上の水でテストを実施。データの蓄積と条件設定や電極シートの改良など、1年ほど試行錯誤し、有効に水処理ができた5か所での長期実証試験が決まった。しかし、実証試験機が設置されることで製品品質や工場設備に悪影響を及ぼしてはいけないので、試験機設置は一筋縄ではいかない。Iは設置場所や点検フローなど、設置条件を慎重に調査・検討。工場長や製造課・保全課の責任者の協力を得て、現場への負担を考慮しながら実証試験機の仕様を固めていった。5か所同時の実証試験であったため、それぞれの試験状況の確認と改良に、延々と追われることになったが、Iは「ここまできたならやるしかない」と自分を奮い立たせ、実証試験を進めていった。その結果、社内での1年間の耐久テストを経て「排水再利用化」と「純水製造のコスト削減」の2種類実用化の見通しが立った。
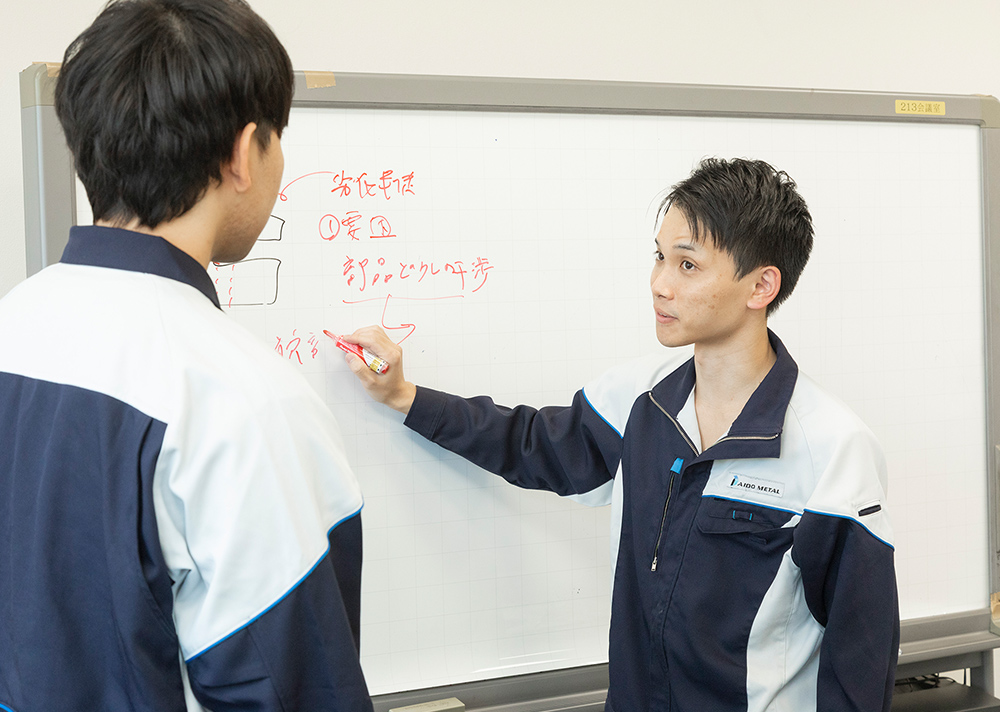
試験機から製品化を目指して
製品化に向けた、外観や操作性を作り込む設計担当に抜擢されたのが、生産技術のTだ。彼がそれまで担当していたのはすべり軸受の加工設備の設計。全く異なる設備の設計に、Iと話し合いながら挑むこととなった。Tは「水処理装置は社内でも初の試みなので、協力会社とも連携して設計を進めました。進めていく中で、疑問点は一つ一つ質問して、設計思想を学びました」と言う。Tは自身初となる流体力学的視点を取り入れ、設計に臨んでいた。この時期にIは、社外に向けて水処理技術のPRを行い、モニター依頼先を探していた。20社以上にPRし、そのうち1社に協力していただけることとなった。Tが操作性やメンテナンス性にもこだわり、ユーザー目線での設計を心掛ける一方で、Iはお客様とのやり取りで出てきた意見をTにフィードバック。連携を取ることでより使いやすい装置にブラッシュアップしている。設計から社外テストの実施までわずか5か月弱。Tは「今にして思うと、失敗を繰り返しながらも経験を積むことができ、多くを学びました」と言う。
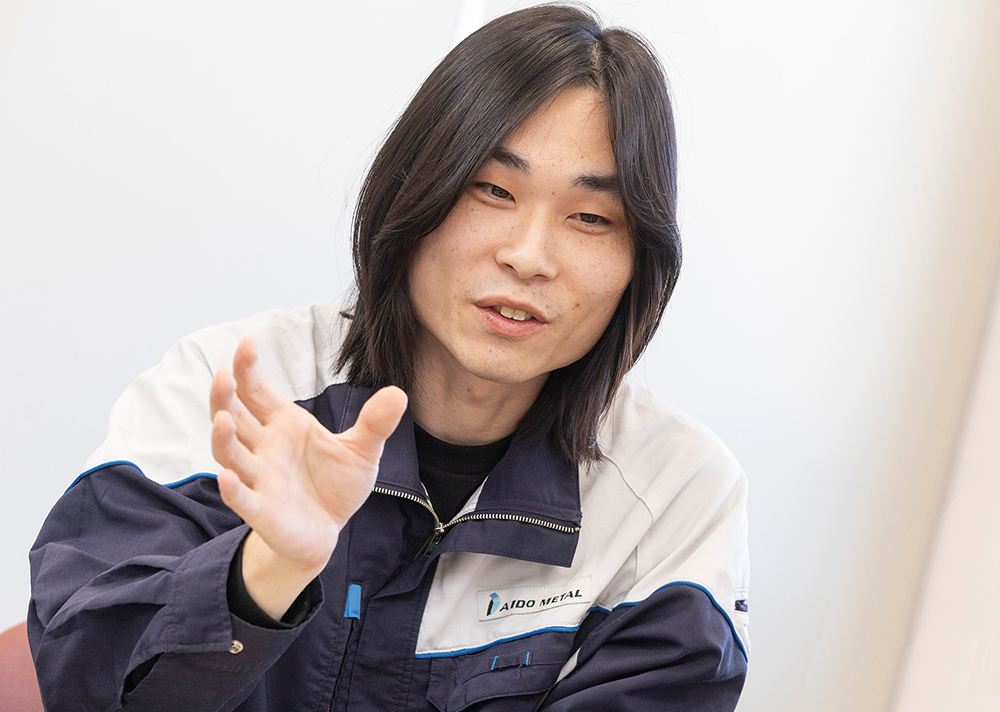
より魅力的な製品設計を
目指して
現在はユーザーにとってより魅力的な製品設計とは何かを突き詰めている最中だ。Tから設計を引き継いだ生産技術のFは、製品化にあたって、よりコンパクトで安全性が高く、コストに配慮した設計を検討。Fは前任のTと同様、Iと密にコミュニケーションを取りながら進めている。実は、Fは入社して3か月でこのプロジェクトに大抜擢。描いた図面とできあがってきた部品がイメージと違う苦労も経験したが、「前職でも経験した生産技術の知見を安全面に盛り込み、全く新しい仕事を楽しんでいます」と笑顔を見せる。
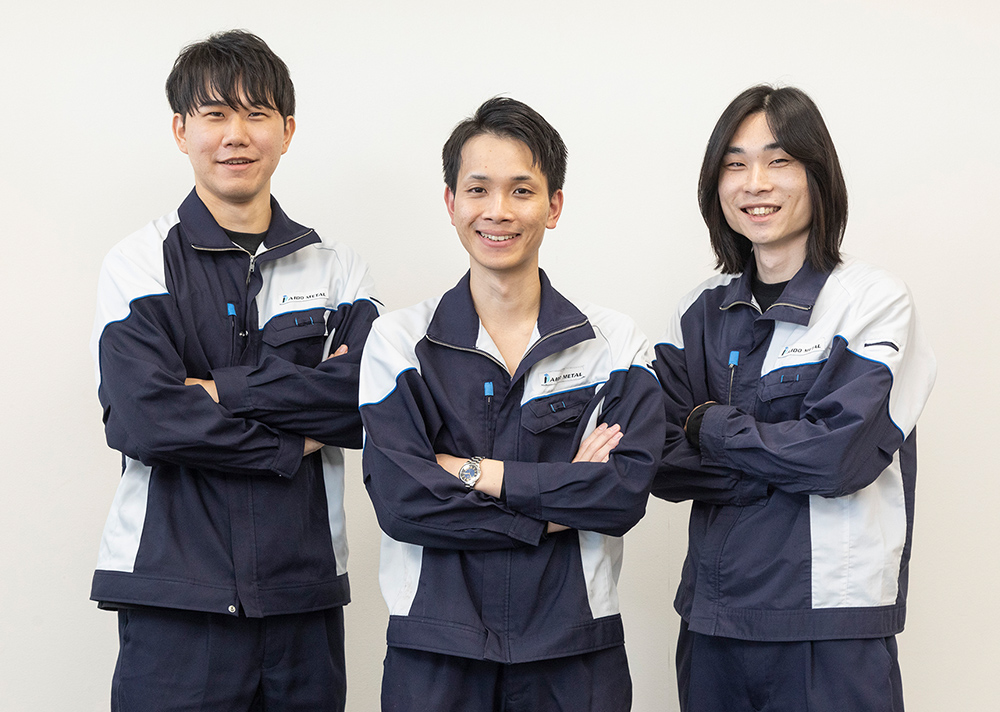
Iは、「水の問題は未来永劫なくなることはない。今はBtoBの用途をメインに進めているが、将来的にはBtoCの用途も視野に入れたい。この水処理技術で会社としてさまざまな形で社会貢献できれば」と思いを語る。大同メタルには、技術者がそんな未来を描いて挑戦できるチャンスがある。
-
Project 02
自動車用部品の
View more
営業開拓